Revolutionizing Business in Electronics and 3D Printing: A Comprehensive Guide to the Concrete Batching Plant Industry
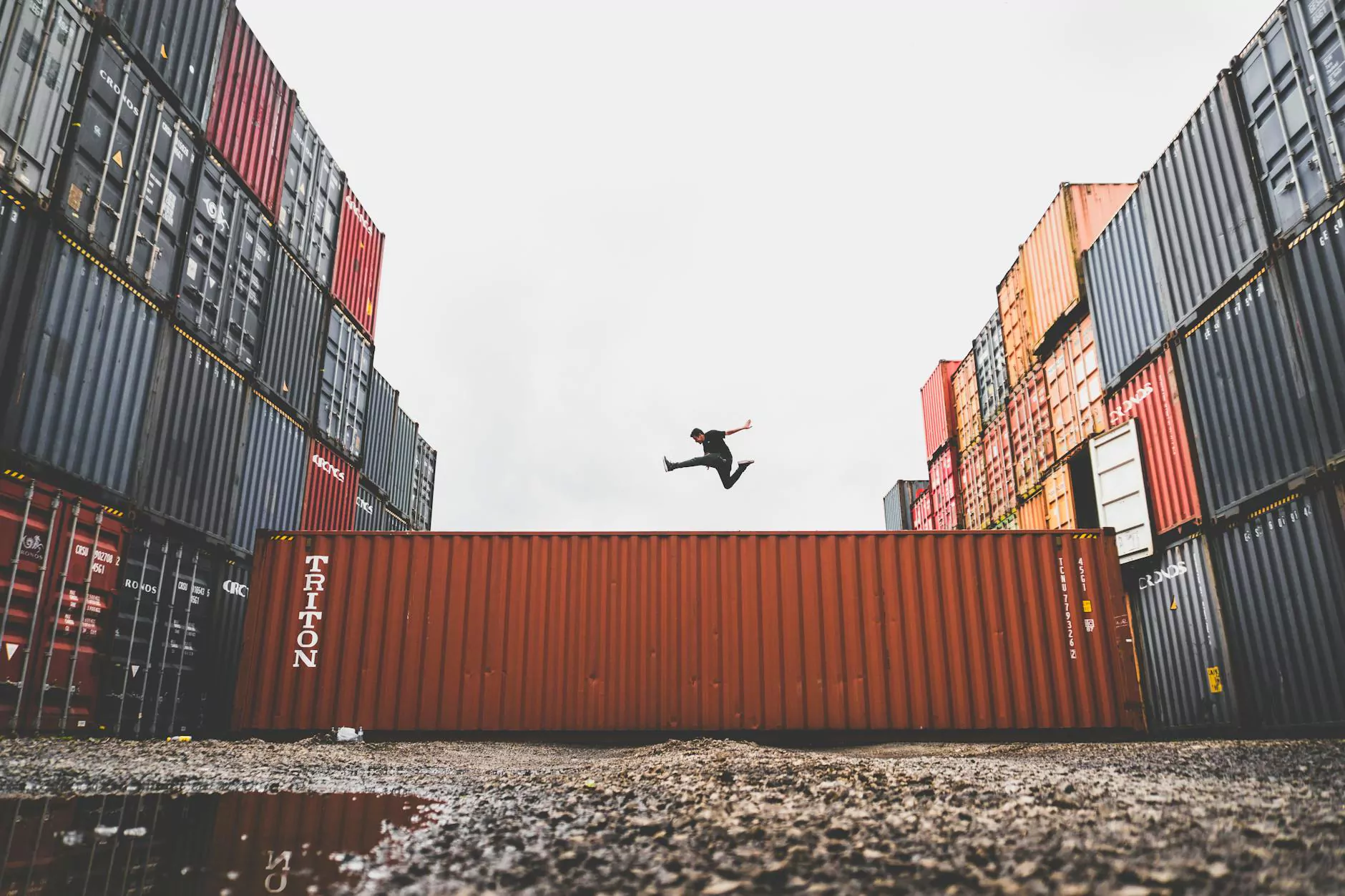
In today's rapidly evolving industrial landscape, businesses that leverage advanced electronics and 3D printing technologies are gaining unprecedented competitive advantages. Within this ecosystem, the concrete batching plant stands out as a vital cornerstone of modern construction services, manufacturing, and infrastructure development. This guide explores how integrating electronics and 3D printing into your concrete batching plant operations can propel your business towards innovation, efficiency, and sustainable growth.
Understanding the Role of Electronics in the Modern Concrete Batching Plant
The cornerstone of any efficient concrete batching plant is its sophisticated electronic control systems. These systems automate critical processes, ensuring precision, reliability, and safety. As the backbone of plant operations, electronics facilitate seamless integration between various mechanical components and operational workflows.
Key Electronic Components in a Concrete Batching Plant
- Programmable Logic Controllers (PLCs): These ideal controllers manage the sequence of operations, monitor sensors, and adapt to real-time conditions, ensuring accurate batching and mixing.
- Human-Machine Interfaces (HMIs): User-friendly touchscreens that enable operators to control and monitor the plant efficiently, providing instant feedback and operational adjustments.
- Sensors and Actuators: Precision sensors measure material levels, moisture content, and temperature, feeding data to control systems for optimal operation.
- Wireless Communication Modules: Facilitate remote operation, real-time data collection, and predictive diagnostics, minimizing downtime and maintenance costs.
Integrating cutting-edge electronics into your concrete batching plant not only enhances operational efficiency but also boosts safety protocols and minimizes human error. Automated electronic systems are pivotal in achieving high-quality concrete production that meets strict industry standards.
The Transformative Impact of 3D Printing in Concrete Manufacturing
3D Printing, also known as additive manufacturing, has revolutionized traditional construction and manufacturing paradigms. In the context of concrete batching plants, 3D printing introduces novel possibilities for creating complex structures, reducing waste, and decreasing construction timelines.
How 3D Printing Enhances the Concrete Industry
- Rapid Prototyping and Customization: 3D printing allows for the rapid production of customized components, molds, and structures, drastically reducing lead times.
- Cost Efficiency: The additive manufacturing process minimizes material waste and decreases labor costs, making projects more economical.
- Design Complexity: 3D printing enables construction of intricate geometries that are difficult or impossible with traditional methods, expanding creative possibilities.
- Sustainable Construction: Utilizing eco-friendly materials and optimizing material usage aligns with green building initiatives, promoting a sustainable future.
Application of 3D Printing in Concrete Batching
Within a concrete batching plant, 3D printing technology can be employed for manufacturing custom molds, precast structural components, and even entire building sections. This integration accelerates project timelines and enhances the precision of concrete elements, benefiting both small-scale projects and large infrastructure undertakings.
Synergizing Electronics and 3D Printing for Business Excellence
The convergence of electronics and 3D printing technologies opens new avenues for business growth and operational excellence in the concrete batching plant industry. Here are key strategies to harness this synergy:
Enhanced Design and Manufacturing
Utilize 3D printing for rapid prototyping of electronic components, custom control panels, or specialized parts, facilitating quick iterations and innovation.
Automation and Smart Operations
Integrate electronic sensors with 3D printed components for advanced diagnostics and predictive maintenance, reducing downtime and ensuring consistent product quality.
Customization and Flexibility
Design custom molds and structural elements via 3D printing, tailored specifically for your project requirements, thus offering bespoke solutions and differentiating your business in a competitive market.
Key Benefits of Innovation in the Concrete Batching Plant Sector
Adopting advanced electronics and 3D printing technologies yields several tangible benefits for businesses involved in the concrete batching plant industry:
- Increased Production Efficiency: Automation and precise electronic control systems streamline operations, boosting throughput and reducing waste.
- Higher Quality and Consistency: Electronic monitoring ensures precise batching, leading to superior concrete quality and compliance with standards.
- Cost Savings: Reduced material waste, lowered labor costs, and optimized operational workflows translate into better profit margins.
- Innovation Leadership: Pioneering the integration of electronics and 3D printing positions your business as an industry leader, attracting new clients and partnerships.
- Sustainability: More eco-friendly manufacturing processes and green building practices support environmental stewardship and social responsibility.
Guidelines for Implementing Advanced Technologies in Your Business
To fully capitalize on electronics and 3D printing in the concrete batching plant domain, consider the following strategic steps:
- Investment in Research and Development: Allocate resources to research innovative electronic control systems and 3D printing materials suitable for concrete applications.
- Partner with Industry Leaders: Collaborate with pioneers like polygonmach.com to access state-of-the-art technology, engineering expertise, and reliable support.
- Training and Skill Development: Provide comprehensive training for your staff on new electronic systems and 3D printing techniques to maximize operational efficiency.
- Adopt Sustainable Practices: Focus on eco-friendly materials and waste reduction to align with global sustainability trends.
- Continuous Innovation: Stay updated on technological advancements to refine your processes, products, and services continually.
Conclusion: Embracing the Future of Business with Technology
In the fast-paced world of construction, manufacturing, and electronics, the integration of electronics and 3D printing into concrete batching plant operations is not just a trend—it's a strategic necessity. These technologies empower businesses to achieve unprecedented efficiency, precision, and innovation. By embracing these advancements, you position your enterprise at the forefront of the industry, capable of delivering high-quality products faster, cheaper, and more sustainably than ever before.
Leading companies like polygonmach.com exemplify how combining technological expertise with industry knowledge creates compelling solutions that transform the concrete batching plant landscape. Whether you are expanding into electronics, investing in 3D printing, or integrating both, remember that the future belongs to those who innovate.
Final Thoughts: Building a Sustainable and Prosperous Future in the Business of Concrete
Innovation in electronics and 3D printing offers a pathway to not only optimize concrete batching plant processes but also to differentiate your business in a competitive marketplace. By prioritizing continuous improvement, leveraging the latest technologies, and fostering a culture of innovation, your enterprise can achieve sustainable success, deliver exceptional value to clients, and contribute positively to global industry trends.
Empowering your business with the most advanced tools and strategies ensures resilience, agility, and long-term profitability—essentials for thriving in today's dynamic industrial environment.