Unlocking the Potential of Plastic Injection Mold Makers
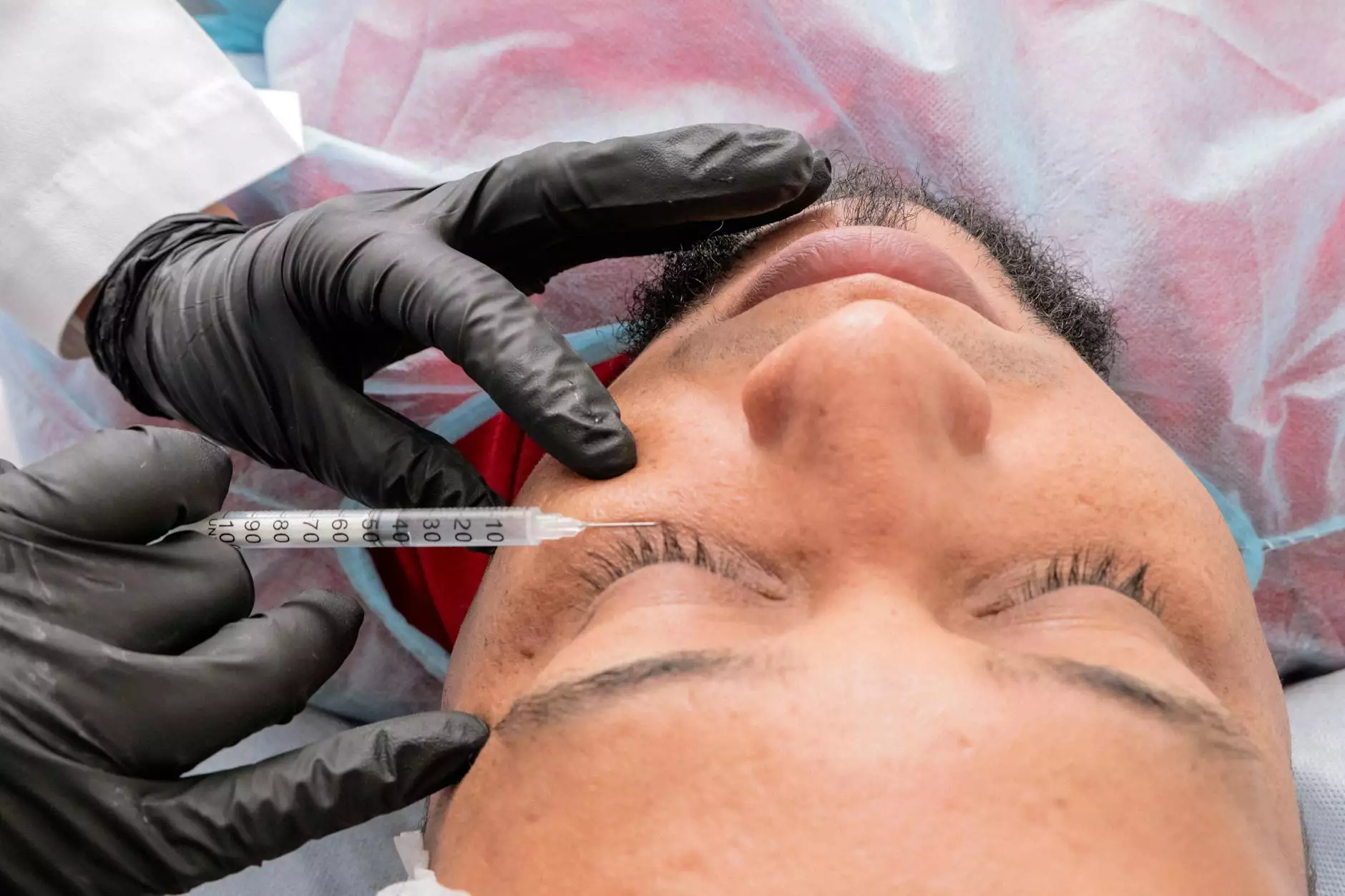
The realm of manufacturing has continually evolved over decades, but plastic injection mold makers stand out as pivotal contributors to modern product development. Their expertise transforms raw materials into intricate, high-quality components that cater to diverse industries ranging from automotive to consumer goods. In this article, we delve deep into the intricacies of plastic injection molding, examining its benefits, processes, challenges, and the vital role of mold makers.
Understanding Plastic Injection Molding
Plastic injection molding is a manufacturing process used to produce parts by injecting molten material into a mold. The process involves several critical steps, including:
- Designing the Mold: The first step is to create a reliable design that considers part geometry and material properties.
- Manufacturing the Mold: Precision is vital in this stage; often, CNC machines are utilized.
- Material Selection: Choosing the right plastic material plays a significant role in the final product's durability.
- Injection Process: The molten plastic is injected into the mold and allowed to cool and solidify.
- Trimming and Finishing: Once cooled, excess materials are trimmed, and the part is finished according to specifications.
The efficiency of this entire operation is largely contingent upon the craftsmanship of a plastic injection mold maker.
The Significance of Plastic Injection Mold Makers
Plastic injection mold makers are the unsung heroes of product development. Their skilled craftsmanship ensures that every mold produced meets precise specifications, leading to high-quality results. Here are some significant aspects of their role:
- Expertise: Skilled mold makers possess in-depth knowledge of materials, design principles, and manufacturing techniques.
- Innovation: They are problem solvers who can innovate solutions for complex manufacturing challenges.
- Quality Assurance: Their dedication to quality ensures the mold will produce parts that meet the highest standards.
Advantages of Plastic Injection Molding
The advantages of utilizing plastic injection mold makers and the molding process are vast and impactful. Here are some notable benefits:
1. High Efficiency
Once a mold is designed and built, it can produce thousands of identical parts efficiently. This streamlined process greatly reduces labor time and costs associated with manufacturing.
2. Complex Designs
Injection molding allows for the creation of very detailed and intricate designs that would be impossible or prohibitively expensive through other manufacturing methods.
3. Material Versatility
A wide variety of plastic materials can be used, including thermoplastics, thermosetting polymers, and elastomers, providing manufacturers with various options for different applications.
4. Waste Reduction
This process is inherently less wasteful than many other manufacturing processes, significantly reducing the environmental footprint.
The Process in Detail
Design Phase
The design phase is crucial for successful plastic injection molding. Here, the following tasks are typically performed:
- CAD Modeling: Computer-Aided Design (CAD) models are developed to visualize and refine component specifications.
- Prototype Testing: Rapid prototyping techniques are adopted to test and validate designs before mold production.
Mold Construction
After approving the design, the mold construction phase begins. This includes:
- Material Selection: The mold is typically made from high-strength steel or aluminum to withstand the high pressure and temperature during the injection process.
- CNC Machining: Computerized numerical control (CNC) machines are employed to create the precise cavity shapes required.
Injection Phase
Once the mold is ready, the injection phase begins:
- Heating the Plastic: Plastic pellets are heated until they become molten and can be injected into the mold.
- Filling the Mold: The molten plastic is injected into the mold under high pressure, ensuring that it fills every crevice.
- Cooling: The mold is cooled, allowing the plastic to solidify into the desired shape.
Final Touches
After cooling, the mold is opened, and the finished parts are ejected. The additional steps may include:
- Trimming: Removing excess plastic, if needed.
- Surface Finishing: Applying various treatments to enhance the appearance and durability of the parts.
Challenges Faced by Plastic Injection Mold Makers
While the benefits are substantial, plastic injection mold makers also face several challenges:
- Design Complexity: As product designs become more intricate, the challenges associated with mold design and manufacturing increase significantly.
- Material Limitations: Not all materials lend themselves well to injection molding, necessitating careful selection and testing.
- Maintaining Precision: The requirement for tolerances is tight; deviations can lead to parts that do not fit or function as desired.
- Cost Management: High initial costs of mold-making demand careful financial planning and forecasting.
The Impact on Various Industries
Plastic injection molding has found significant applications across diverse industries:
Automotive Industry
Automakers use injection-molded components for parts such as dashboards, bumpers, and interior trims, focusing on reducing weight while improving strength and durability.
Consumer Products
Household goods, packaging, and electronics heavily rely on injection molding for producing standardized yet diverse parts.
Medical Industry
The rise of medical device manufacturing has led to the increased demand for high-quality, sterile, and precise plastic components, where injection molding fulfills the stringent regulations.
Future Trends in Plastic Injection Molding
As technology advances, the field of plastic injection mold making continually evolves. Here are some key trends:
- Automation: The integration of robotics and automation within the manufacturing processes enhances efficiency and reduces labor costs.
- 3D Printing: The adoption of 3D printing for prototyping is revolutionizing traditional mold design, allowing for quicker iterations and lower costs.
- Sustainability Practices: Manufacturers are increasingly seeking eco-friendly materials and practices to reduce waste and improve overall sustainability in production.
Conclusion
In summary, the role of a plastic injection mold maker is integral to modern manufacturing. With their specialized skills, they ensure the creation of high-quality molds that lead to efficient production processes, contributing to the success of various industries. As the demand for plastic parts grows, so too does the importance of continuous innovation and excellence in mold-making practices. By understanding the complexities, advantages, and future trends associated with plastic injection molding, businesses can harness its full potential to meet market demands while remaining competitive.
For more information, please visit DeepMould.net.