Making Carbon Fiber Body Panels: A Comprehensive Guide
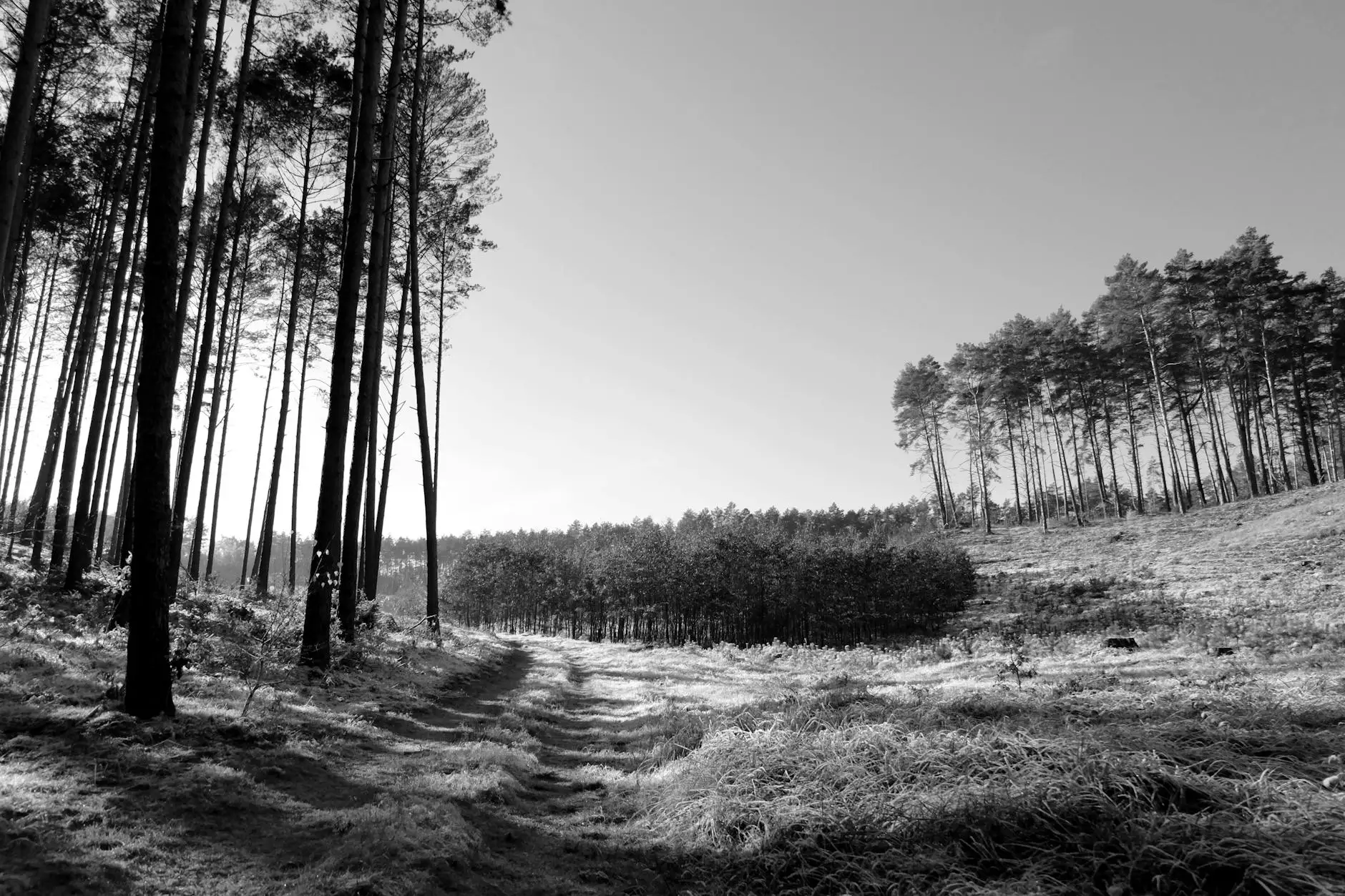
In the world of automotive customization, one material has emerged as a game-changer: carbon fiber. Known for its lightweight strength and incredible durability, carbon fiber is revolutionizing the industry, particularly in the creation of carbon fiber body panels. This article will delve into the process of making carbon fiber body panels, their benefits, and their impact on automotive performance and aesthetics.
What is Carbon Fiber?
Carbon fiber is a high-performance material made from thin strands of carbon atoms. These strands are woven together and then infused with resin to create a composite that is both incredibly strong and lightweight. Due to its unique properties, carbon fiber is widely used in various industries, including aerospace, sports equipment, and of course, automotive manufacturing.
The Advantages of Carbon Fiber Body Panels
Choosing carbon fiber body panels for automotive applications comes with a multitude of benefits:
- Weight Reduction: Carbon fiber is significantly lighter than traditional materials like steel or aluminum, leading to improved fuel efficiency and handling.
- Enhanced Performance: The reduced weight allows for better acceleration, braking, and cornering, making vehicles more responsive.
- Durability: Carbon fiber panels resist corrosion and damage better than metal, ensuring longer-lasting vehicles.
- Aesthetic Appeal: The glossy finish of carbon fiber panels gives a modern, high-tech look that many automotive enthusiasts desire.
- Customization: Carbon fiber can be molded into various shapes and sizes, offering endless possibilities for auto customization.
The Process of Making Carbon Fiber Body Panels
Creating carbon fiber body panels involves several key steps, each requiring precision and expertise. Here’s an in-depth look at the process:
1. Design and Prototyping
The first step in making carbon fiber body panels is designing the part. Using Computer-Aided Design (CAD) software, engineers create detailed models of the body panels. This stage is crucial as it allows for adjustments before moving on to production. Prototyping often involves 3D printing or creating molds from the CAD files.
2. Material Selection
Choosing the right type of carbon fiber is critical. Manufacturers can select from various grades and weaves of carbon fiber. The choice depends on the desired strength, flexibility, and weight of the end product. Common choices include:
- Prepreg Carbon Fiber: Pre-impregnated with resin, offering excellent strength and consistency.
- Woven Carbon Fiber: Provides unique aesthetics and properties tailored for specific applications.
- Chopped Carbon Fiber: Suitable for bulk applications where less structural integrity is needed.
3. Creating Molds
Once the design is finalized, molds are created to shape the carbon fiber. These molds can be made from aluminum, fiberglass, or composite materials and are designed to the exact specifications of the desired body panel. The quality of the mold plays a significant role in the final product's smoothness and finish.
4. Layup Process
The next step is the layup process, where layers of carbon fiber fabric are laid up in the mold. Typically, several layers are used to achieve the desired thickness and strength. The layers are often bonded together with resin, and care must be taken to eliminate air bubbles, which can weaken the finished panel.
5. Curing
After the layup, the assembly is subjected to a curing process. This can be done at room temperature or using an autoclave (high-pressure oven) for quicker and more effective results. Curing hardens the resin, creating a solid panel. The temperature and duration of this process are critical for achieving the desired mechanical properties.
6. Finishing Touches
Once curing is complete, the panels are removed from the mold. Further finishing processes, such as sanding, trimming, and coating, are applied to achieve a smooth, glossy finish. Optional protective coatings can also be added to enhance UV resistance and longevity.
The Impact of Carbon Fiber Body Panels on the Automotive Industry
The introduction of carbon fiber body panels is reshaping the automotive landscape. Here’s how:
1. Performance Vehicles
High-performance vehicles from leading manufacturers have increasingly adopted carbon fiber body panels to achieve maximum performance. By significantly reducing weight, these vehicles can accelerate faster and handle better, making them more appealing to enthusiasts.
2. Sustainable Practices
As the automotive industry shifts towards sustainability, carbon fiber offers a promising solution. Its lightweight nature contributes to improved fuel economy, reducing emissions and energy consumption. Additionally, advancements in recycling technology for carbon fiber composites are slowly paving the way for more sustainable practices.
3. Enhanced Safety
Interestingly, carbon fiber is not just about performance—it also enhances safety. Its high strength-to-weight ratio allows for improved structural integrity during collisions, providing better protection for vehicle occupants.
Challenges in Making Carbon Fiber Body Panels
While making carbon fiber body panels has many advantages, there are challenges that manufacturers face:
- Cost: The production of carbon fiber is more expensive than traditional materials, which can raise the vehicle's overall cost.
- Complexity of Manufacturing: The process of laying up and curing carbon fiber requires specialized skills and equipment, challenging for smaller manufacturers.
- Public Perception: Some consumers remain unaware of the benefits of carbon fiber, leading to hesitation in adoption.
The Future of Carbon Fiber in Automotive
The future of carbon fiber body panels in the automotive industry looks promising. As technology continues to advance, the cost of production is expected to decrease, making this material more accessible. Furthermore, innovations in manufacturing techniques, such as automated lay-up systems and improved recycling methods, will likely increase efficiency and sustainability.
1. Broader Applications
More automotive manufacturers are slowly recognizing the advantages of carbon fiber, leading to broader applications beyond high-performance vehicles. We can expect to see standard production vehicles incorporating carbon fiber components for enhanced efficiency and performance.
2. Customization Opportunities
The rise of customization among car enthusiasts signifies a growing market for carbon fiber body panels. As consumers seek to express their individuality, the demand for unique, lightweight body panels will continue to rise.
3. Innovation and Research
Research into new carbon fiber composites and technologies is ongoing. This includes exploring alternatives to traditional resin systems and developing new methods for integrating carbon fiber into existing manufacturing processes.
Conclusion
In conclusion, making carbon fiber body panels represents a significant advancement in the field of automotive customization. The combination of lightweight strength, durability, and aesthetic appeal positions carbon fiber as a material at the forefront of the automotive industry. As technology progresses and costs decline, we can expect this innovative material to become even more prevalent in vehicles of all types. The future of automotive performance, customization, and sustainability is undeniably intertwined with the potential that carbon fiber presents.
As enthusiasts and manufacturers alike embrace the benefits of carbon fiber, the automotive landscape will continue to evolve, making it an exciting time for both the industry and consumers interested in cutting-edge technology.