Understanding Precision Mold Components in Metal Fabrication
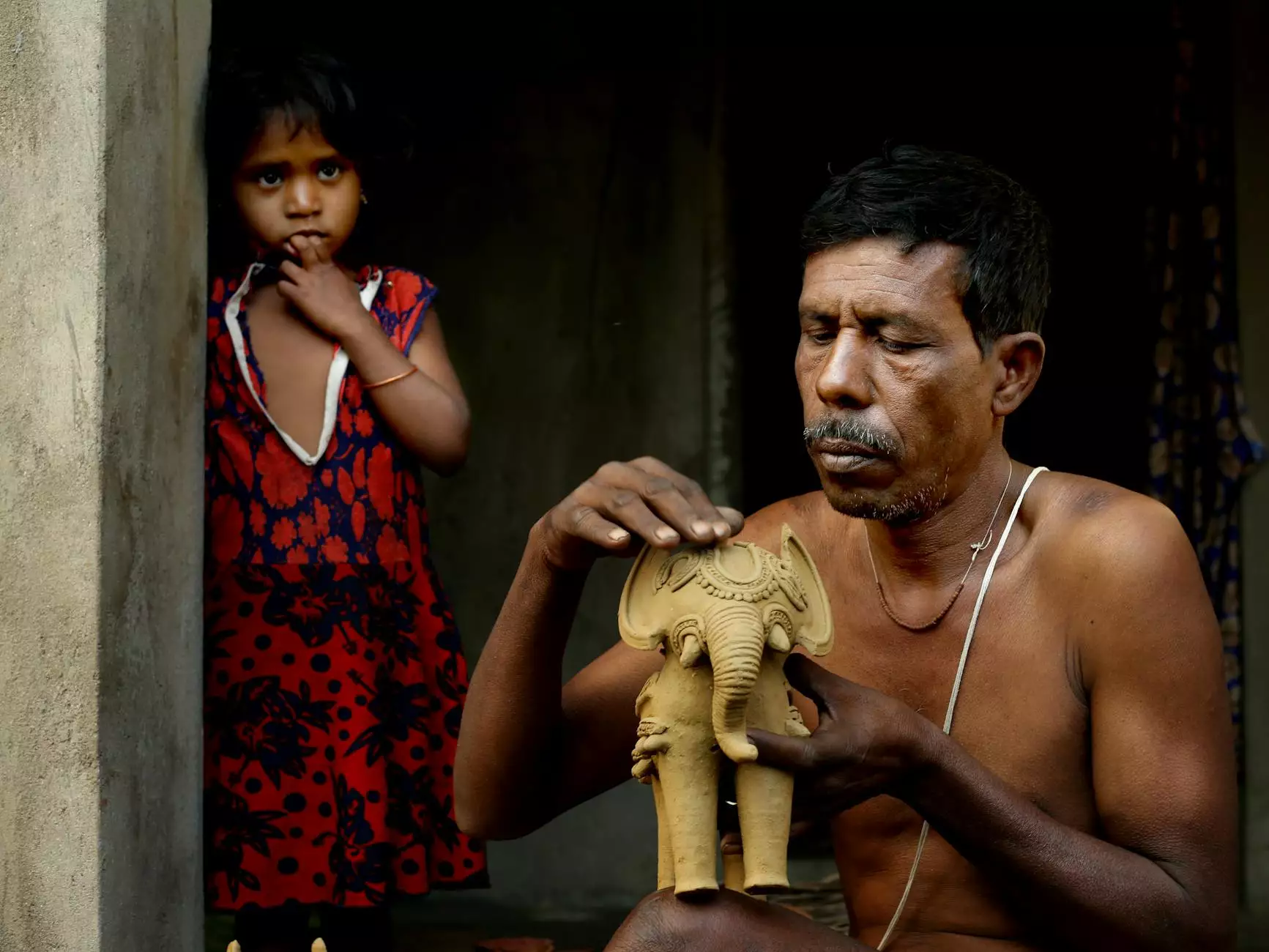
In the realm of metal fabrication, the importance of precision mold components cannot be overstated. These components play a vital role in the manufacturing process, influencing the quality and efficiency of the final products. In this lengthy exploration, we will dive deep into what precision mold components are, their applications, benefits, and much more, providing you a comprehensive understanding of their significance in modern manufacturing.
What Are Precision Mold Components?
Precision mold components refer to the parts used in molds for various manufacturing processes, such as injection molding, die casting, and compression molding. These components are meticulously crafted to meet stringent specifications, ensuring that they deliver high repeatability and reliability in the production of parts across various industries.
Core Elements of Precision Mold Components
The core elements that define precision mold components include:
- Design Accuracy: The design process is crucial to ensure that mold components meet the required specifications and tolerances.
- Material Selection: Different applications demand various materials, such as hardened steel or aluminum, each impacting durability and performance.
- Manufacturing Process: Advanced manufacturing techniques, like CNC machining and wire EDM, are employed to achieve high precision levels.
- Surface Finish: A high-quality surface finish is essential to prevent defects in the molded products and to enhance durability.
The Importance of Precision Mold Components
Precision mold components are crucial for numerous reasons:
- Enhanced Quality: High-quality mold components lead to better-quality finished products. Any imperfection in the mold can result in defects in the final product.
- Cost Efficiency: Investing in precision components reduces waste and errors, thus lowering overall production costs.
- Reliability: Consistent performance of molds created with precision components leads to reliable manufacturing processes.
- Increased Production Speed: High-precision molds ensure that the manufacturing processes run smoothly and quickly, thus enhancing overall productivity.
Applications of Precision Mold Components
The applications of precision mold components span a wide range of industries:
- Aerospace: In this highly regulated industry, precision molds are critical for producing complex components with strict tolerance requirements.
- Automotive: From dashboards to engine components, precision molds facilitate the creation of reliable parts crucial for safety and performance.
- Consumer Electronics: Molding components for devices like smartphones and laptops require precise mold parts to ensure a perfect fit and finish.
- Medical Devices: The production of medical instruments and devices mandates the highest standards of precision to maintain safety and efficacy.
Choosing the Right Precision Mold Components
Selecting the right precision mold components involves several considerations. Here is what to keep in mind:
- Manufacturing Volume: Understand your production volume requirements. Some molds are better suited for high-volume runs, while others are tailored for low volume or custom jobs.
- Material Compatibility: Ensure that the selected components are compatible with the materials you intend to use in the molding process.
- Budget Constraints: While precision molds are an investment, it is critical to evaluate all options to find a balance between quality and cost.
- Provider Reputation: Working with a reputable mold manufacturer is key to ensuring quality and support throughout the process.
Metal Fabricators and Precision Mold Components
Metal fabricators are central to the production of precision mold components. These professionals specialize in shaping and assembling metal parts, which are then utilized in various manufacturing processes. The synergy between metal fabrication and precision molds is crucial for achieving the desired specifications and performance characteristics. Deepmould.net is a leading provider in this niche, offering top-notch services for the fabrication and design of precision mold components.
Key Services Offered by Metal Fabricators
Metal fabricators typically offer a range of services that support the creation of precision mold components, including:
- CNC Machining: Utilizing advanced computer-controlled machines to create high-accuracy mold parts with intricate designs.
- Welding: Efficiently joining different metal components to form complete mold assemblies.
- Finishing Services: Applying surface treatments such as polishing, coating, or painting to increase durability and aesthetics.
- Prototyping: Developing prototypes for testing purposes before commencing mass production.
The Process of Creating Precision Mold Components
The journey of creating precision mold components typically follows these steps:
1. Design Phase
The first step involves a detailed design phase, where engineers and designers collaborate using CAD software to create accurate models of the mold components.
2. Material Selection
Your choice of material directly affects the performance and durability of precision mold components. Steel, aluminum, and certain alloys are common choices based on the application.
3. Manufacturing Phase
Using techniques such as CNC machining, metal fabricators fabricate the components to precise specifications. This process often includes various machining operations such as milling, turning, and drilling.
4. Quality Assurance
Following manufacturing, rigorous quality checks are performed. This ensures that the components meet the set tolerances and standards.
5. Assembly
Assemblies are put together to form the final mold, ready for production runs. Proper assembly further contributes to the precision and efficacy of the final products.
Trends and Innovations in Precision Mold Components
The landscape of precision mold-making is continually evolving, marked by innovative trends such as:
- Additive Manufacturing: Also known as 3D printing, this technique is transforming aspects of mold making by allowing for intricate designs that were previously impossible.
- Smart Manufacturing: Incorporating IoT technologies to monitor and optimize the manufacturing processes in real-time.
- Sustainable Practices: Greater emphasis on recycling materials and reducing waste spikes as businesses focus on sustainability.
Conclusion: The Future of Precision Mold Components
In conclusion, precision mold components are integral to the success of various manufacturing industries. They promise enhanced product quality, cost savings, and expanded capabilities. As advancements in technology continue to emerge, so will the opportunities for innovation in the field of mold components. Investing in high-quality precision molds from reputed manufacturers such as Deepmould.net will not only enhance production efficiency but also ensure ongoing competitiveness in rapidly evolving markets.